온실가스를 이용해 수소나 일산화탄소처럼 유용한 가스를 만드는 ‘합성가스 촉매 기술’이 나왔다. 상업화를 위한 여러 조건도 만족해 상용화 가능성도 커졌다.
에너지화학공학과의 김건태 교수팀은 이산화탄소(CO₂)와 메탄(CH₄)을 수소(H₂)나 일산화탄소(CO) 등의 유용한 합성가스로 전환하는 ‘더 좋은 촉매 기술’을 개발했다. 이 촉매의 합성가스 전환효율은 95% 이상이며, 기존처럼 성능을 높이기 위해 주입하던 다른 가스가 없어도 1,000시간 동안 구동할 수 있다.
김건태 교수는 “그동안 온실가스를 수소로 변환하는 시도는 여러 차례 있었지만 적합한 촉매를 개발하지 못해 번번이 상업화에 실패했다”며 “이번 연구로 상업화를 위한 모든 요건을 만족한 만큼 상용화에 속도가 붙을 것”이라고 전망했다.
합성가스는 채굴이 아닌 화학적 합성으로 확보한 가스 자원을 뜻한다. 합성가스 시장은 2022년 60조 원 규모이며, 2028년에는 88조 원 규모로 예상된다. 이처럼 시장수요는 빠르게 증가하고 있지만, 핵심기술은 해외기업이 보유하고 있어 국산화가 쉽지 않았다. 최근 국내 대기업들이 합성가스의 중요도를 체감하며, 합성가스 시장에 진출을 준비하고 있다.
김 교수는 “이번에 개발한 기술은 합성가스 기술의 국산화 시도에 큰 교두보 역할을 할 것”이라며 “합성가스 생산에 지구온난화의 주범인 이산화탄소를 대량 활용하는 점도 큰 특징”이라고 설명했다.
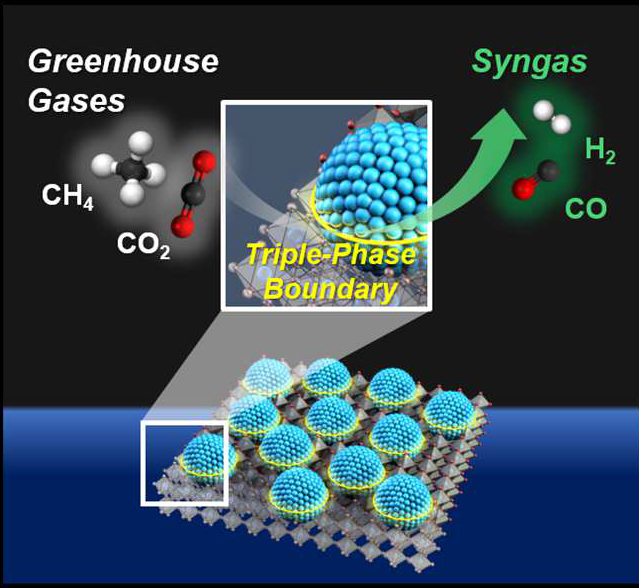
용출 나노 촉매를 이용해 온실가스를 합성가스로 생산하는 모형. 메탄과 이산화탄소를 새로운 촉매와 함께 넣은 다음 전기를 흘리면 수소나 일산화탄소 같은 유용한 합성가스를 생산할 수 있다.
새로운 촉매는 철(Fe)과 니켈(Ni)을 바탕으로 한 전이금속이 주성분이며, 귀금속을 전혀 포함하지 않아 가격이 저렴하다. 니켈 성분은 기존처럼 덩어리(bulk) 형태가 아니라 고밀도 나노 입자로 페로브스카이트 지지체 표면에 올라오게 된다. 이 덕분에 촉매 표면에서 니켈 입자가 뭉치거나 움직이지 않아 반응성이 유지된다.
기존에는 반응성을 유지하기 위해 메탄과 이산화탄소뿐 아니라 질소나 아르곤, 헬륨, 수증기 등의 희석가스를 함께 주입했다. 그러나 이런 공정을 추가하거나 추후 가스 분리에 들어가는 비용이 많아서 상업화 측면에서 손해가 컸다. 연구진은 이런 걸림돌을 촉매 내부의 니켈 입자가 표면으로 스스로 솟아나오는 ‘스마트 자가재생(용출, exsolution)’ 기법으로 풀었다. 촉매 표면에 새로운 니켈 나노 입자가 재생되면서 촉매 성능이 오래 유지되도록 한 것이다.
제1저자인 오진경 연구원은 “기존에 쓰이던 니켈 금속 기반의 촉매는 초기 성능이 우수하지만, 고온에서 촉매 입자끼리 뭉치고 반응을 반복할수록 고체 탄소가 촉매 표면에 쌓여(탄소 코킹) 반응성이 낮아진다”며 “이번에 개발한 촉매는 니켈 입자의 ‘용출 현상’을 이용해 이런 문제들을 해결했다”고 설명했다.
김건태 교수는 “메탄 건식 개질 반응을 통해 비용을 적게 들이면서 안정적으로 합성가스와 수소를 생산하려면 촉매 활성과 안정성, 그리고 희석가스가 없는 공정이 뒷받침돼야 한다”며 “이번 연구로 이런 여러 조건을 동시에 만족하는 촉매 물질을 개발해 매탄 건식 개질 상용화에 크게 기여할 것”이라고 기대했다.
이번 연구에는 포항공대 화학공학과 한정우 교수도 함께 참여했다. 연구 결과는 화학 분야의 세계적 권위지인 ‘앙게반테 케미(Angewandte Chemie International Edition)’에 5월 30일자 온라인 속보로 공개됐으며, 출판을 앞두고 있다.