Lightweight and durable composites are still the dominant materials in aerospace application. A team of researchers from UNIST has reported developing a new composite manufacturing technique, that is not only cheaper, but also simpler and more environmentally friendly.
The team, led by Professor Young-Bin Park and Professor Wooseok Ji in the School of Mechanical Aerospace and Nuclear Engineering at UNIST, has been selected to lead a government-funded aerospace R&D project, together with Korea Aerospace Industries (KAI). This research project is part of the Development Project of Advanced Process Technologies for Aircraft Parts by the Ministry of Trade, Industry and Energy (MOTIE). The research team will receive up to KRW 10 billion in research funding over the five-year period, starting in July 2019.
Under the topic of Development of 4 Meter or Longer Integrated Composite Skin·Stringer Module and 3 Meter or Longer Thermoplastic Composite Fuselage Module for Single Aisle Commercial Aircraft Based on the AFP and OOA Processes, the research team will carry out window frame production, using recycled thermoplastic composites. Through this, they will develop technologies to produce high-quality composite parts, while increasing resource efficiency in the existing composite manufacturing processes.
The composite material currently used in the manufacture of aircraft structures are made from non-recyclable thermoset plastics. However, thermoplastic injection molding requires high heat and high pressure in order to successfully create parts. The equipment used in such process is known as, Autoclave. In general, larger autoclaves are expected for the production of large-scale aircraft components and such equipment is costly and often takes over 10 hours for the epoxy resin to be hardened.
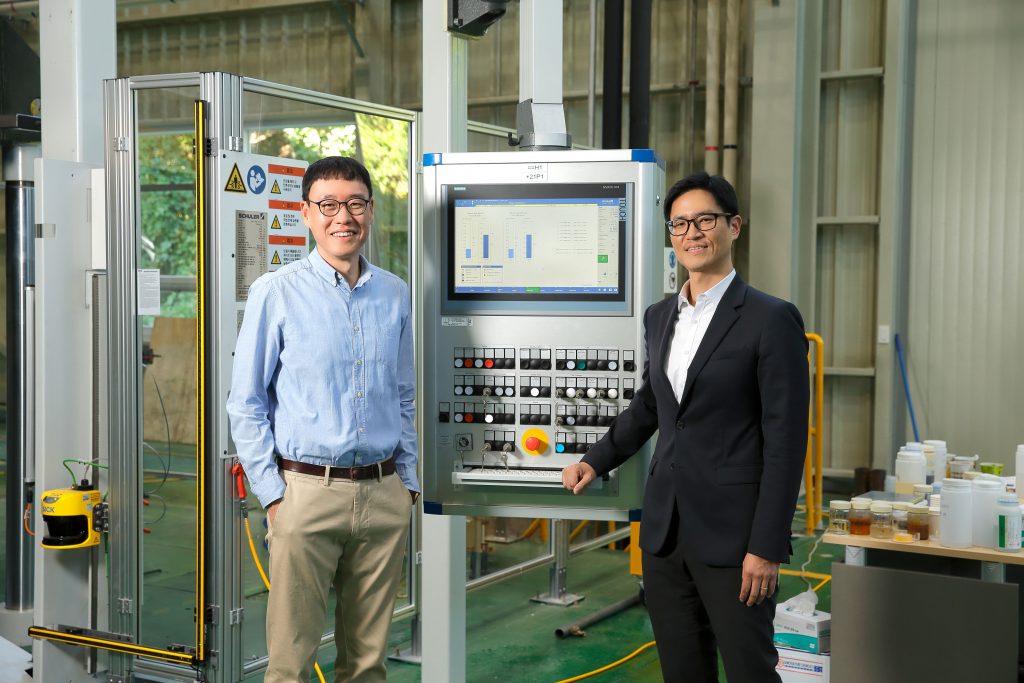
From left are Professor Wooseok Ji and Professor Young-Bin Park in the School of Mechanical Aerospace and Nuclear Engineering at UNIST.
“There are limits to traditional composite molding processes, as thermoset plastics were never designed to be recyclable in the first place. Besides, larger autoclaves are quite poor at managing productivity,” says Professor Ji. “Our research project aims to discard the existing manufacturing process and show innovative eco-friendly materials and enhanced productivity.”
Researchers have set out to develop a novel molding method that could produce parts in minutes using recycled thermoplastic composites. In particular, from basic technology to actual product development, this project is wide ranging. This project magnifies the role of UNIST in that it entails actual product production, rather than merely working on technology development.
The success of joint projects, like this, where universities and businesses work together for the commercialization of outstanding technologies, was largely due to the Fraunhofer Project Center for Composites Research@UNIST (FPC@UNIST) at UNIST.
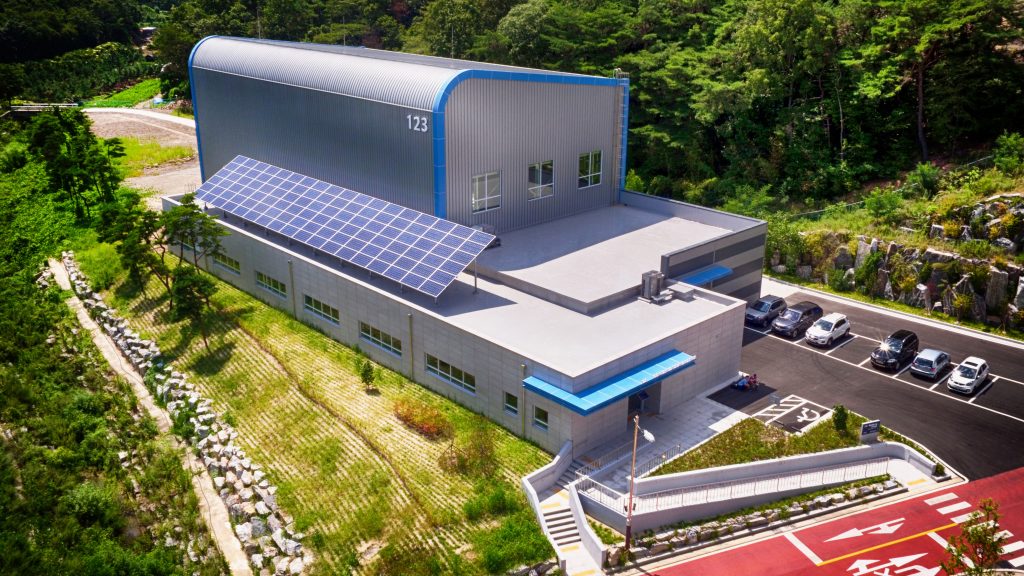
The aerial view of Fraunhofer Project Center for Composites Research@UNIST (FPC@UNIST) at UNIST.
Professor Young-Bin Park, who realized the importance of high-speed molding technology for composites early on, has made constant efforts in laying the groundwork for research and development of lightweight composite materials. This put in place the foundations for the successful launch of the new Korean branch of Fraunhofer research group in 2016. The center has secured a total of KRW 20 billion from the Korean Ministry of Trade, Industry and Energy and the Ulsan city over a period of four years. This new research center is about 1,634 square meters and boasts KRW 10 billion worth high-speed molding equipment for carbon fiber reinforced composites, currently being operated.
“Development of new processes for recycling and remanufacturing composite materials is a crucial research topic being studied in laboratories,” says Professor Park. “Through this project, we plan on developing technologies, capable of recycling of retired aircraft components into new parts, thus making it applicable to other industries where composite materials are used.”