By mimicking the structure of a leaf beetle, researchers have developed a superhydrophobic surface resistant to water droplet impact and pressure. This technology is anticipated to enhance efficiency and reduce maintenance costs across various industries, including marine, aviation, and energy.
Led by Professor Dong Woog Lee in the School of Energy and Chemical Engineering at UNIST, the research team has drawn inspiration from a concave pillar (CP) structure, which is found in the pulvilli of some leaf beetle species and the soil-dwelling springtail (collembola) species. Based on this natural architecture, the team has implemented the CP surfaces that can maintain superhydrophobicity even under harsh environmental conditions.
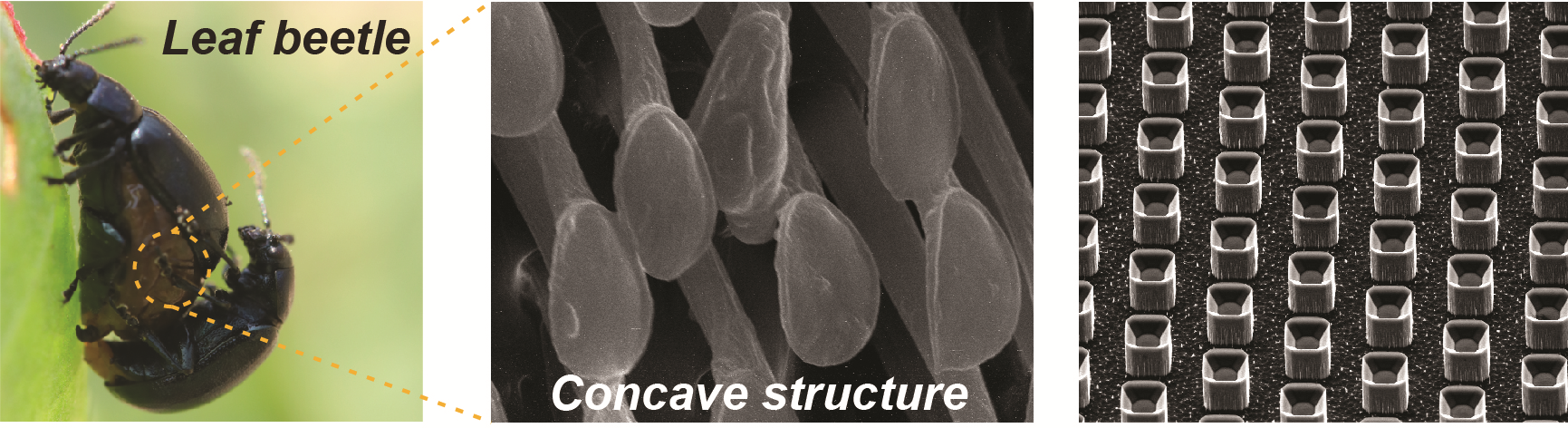
Figure 1. Inceptive design for concave pillar microstructure fabrication.
By leveraging these original structures found in nature, the researchers successfully prevented the droplets from wetting the surface and achieved improved superhydrophobicity. The newly-developed structure has demonstrated significantly greater resistance to impact and water pressure compared to conventional superhydrophobic surfaces.
Superhydrophobicity is defined as the property that allows water to easily roll off without penetrating the surface. This property has numerous applications across various domains, including self-cleaning, anti-icing, and anti-fouling.
Figure 2. Impact pressure-resistant regime of the NP and CP microstructures followed by deducing mechanisms. Shown below is the phase maps of pressure-resistant properties along with NP and CP surfaces as a function of Weber number (We).
Existing superhydrophobic surfaces exhibit limitations, particularly in scenarios where the surfaces get easily wet when shock or pressure is applied to water droplets. To address these challenges, a stable anti-wetting mechanism is essential to maintain superhydrophobicity even in harsh conditions.
The research team utilized the concave structures observed in leaf beetles and soil-dwelling springtails as a basis for their work. By employing this concept, they created the CP surfaces with concave cativities that exhibited stable superhydrophobicity, even when subjected to high-speed water droplet collisions and elevated hydrostatic pressures.
Figure 3. Superior plastron retention property of CP surface. (Left) Mirror-like reflectance of CP surface underwater due to the entrapped air film, plastron. (Right) Saturated plastron (trapped air) after 1440 min, 1 − φ1440, for the NP and CP surfaces as a function of p(h). Dashed curve lines indicate fitted lines for the NP and the CP surfaces, respectively, based on the exponential function. A dashed linear line (at lower p(h)) denotes a fitted line for the CP surface based on the linear function.
Experimental results indicated that the CP structure experienced approximately 1.6 times greater resistance to wetting upon impact compared to the normal pillar (NP) structure. Under high-water-pressure conditions, approximately 87% of the NP structure became wet, whereas only 7% of the CP structure experienced wetting.
The concave cavities generated an air cushion upon contact with water droplets, functioning much like a spring to prevent water penetration. As a result, the CP surface maintained stable superhydrophobicity for over 24 hours.
Professor Lee stated, “We have introduced a new direction for the design of stable superhydrophobic surfaces,” adding that “if this design is successfully implemented, it is expected to make significant contributions across various industrial applications.”
This research involved the contributions of first authors Jinhoon Lee and Jinwoo Park and was supported by the Basic Science Research Program and the Nano & Materials Technology Development Program through the National Research Foundation of Korea (NRF), funded by the Ministry of Science and ICT (MSIT). The findings were published in the online version of Advanced Materials on October 2, 2024.
Journal Reference
Jinhoon Lee, Jinwoo Park, Kwang Hui Jung, et al., “Enhancing Resistance to Wetting Transition through the Concave Structures,” Advanced Materials, (2024).