A team of researchers, affiliated with UNIST has successfully integrated artificial intelligence (AI) technology into the manufacturing process of lithium-ion battery cathode precursors, reducing defect rates and enhancing production efficiency. This advancement is expected to save over 2 billion won annually in production costs.
Led by Professor Im Doo Jung of the Department of Mechanical Engineering and Graduate School of Artificial Intelligence, in collaboration with the Research Institute of Industrial Science & Technology (RIST), the team developed process conditions to lower defect rates in nickel-rich layered oxide (LiNixCoyMnzO2, NCM) precursors. They also devised an AI-powered real-time control system to monitor and adjust the manufacturing process dynamically.
NCM precursors are powdered materials composed of nickel (Ni), cobalt (Co), and manganese (Mn), which are combined at high temperatures to produce cathode material for electric vehicle batteries. While higher nickel content in precursor particles increases battery capacity, it also makes the process prone to nickel leaching—a phenomenon where nickel fails to precipitate properly or dissolves back into the solution. Nickel leaching leads to irregular particle shapes and compositions, ultimately degrading battery performance and lifespan.
To address this challenge, the research team optimized process parameters to suppress nickel leaching and developed an AI-based real-time equipment anomaly detection system. By controlling factors such as stirring speed, pH level, and ammonia concentration, they designed the process so that nickel remains confined within the particle interior, enhancing structural stability and reducing leaching.
Furthermore, the team employed domain adaptation AI technology, significantly improving defect detection performance. Unlike conventional AI models trained solely on laboratory data, domain adaptation AI recognizes and adjusts to environmental and equipment variations during large-scale production, maintaining high prediction accuracy and ensuring consistent quality.
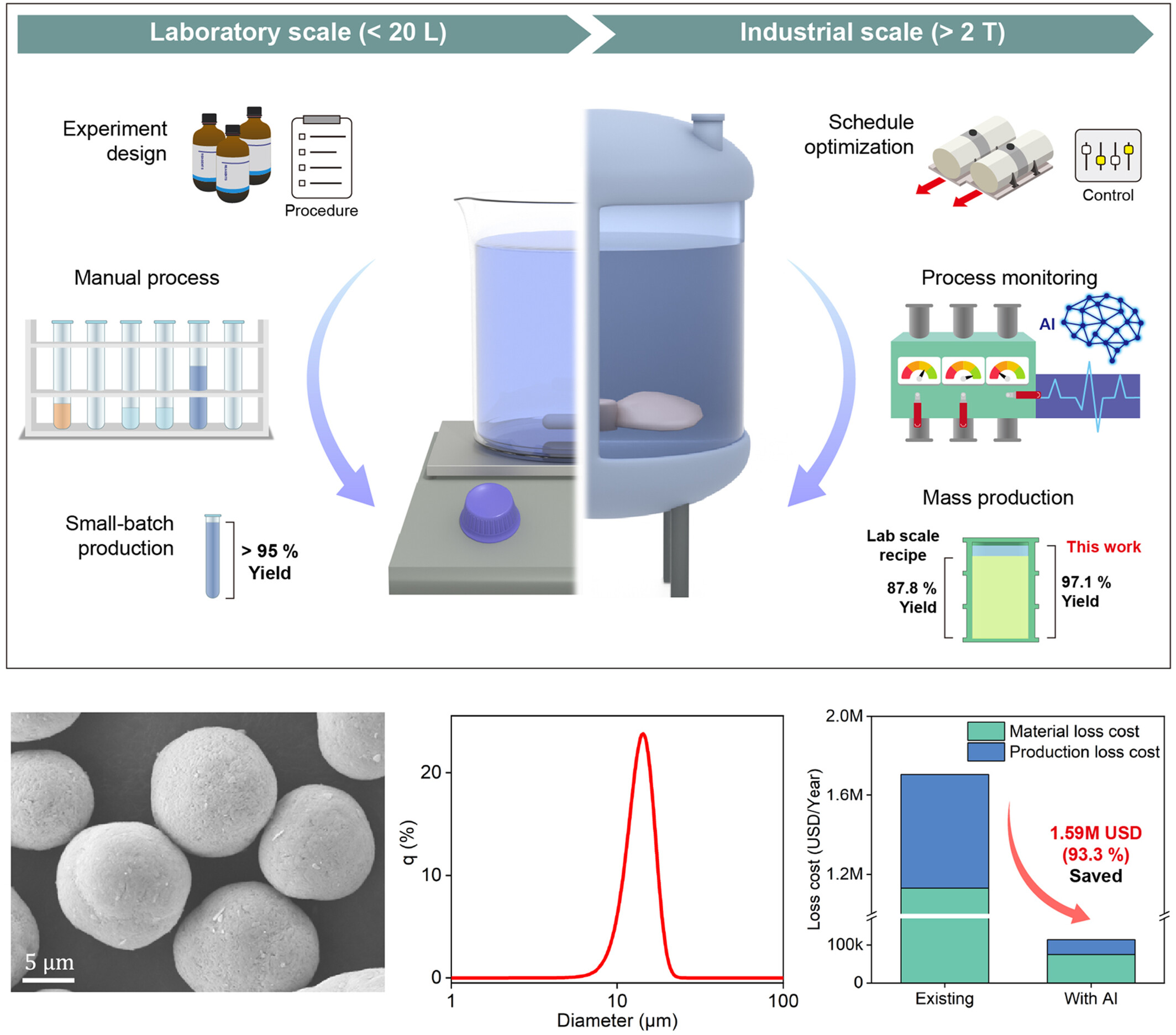
Figure 1. A schematic image, illustrating the overall study.
The research involved Junyoung Seo and Taekyeong Kim from the Department of Mechanical Engineering at UNIST, serving as co-first authors. The team explained, “As equipment ages or production scales up, initial process conditions may drift. Our domain adaptation AI adapts to these changes, ensuring stable, high-quality output.”
The AI system was validated on an industrial-scale 11.5-ton reactor, where it reduced defective batch occurrences to one-fifteenth of previous levels, achieving an anomaly detection accuracy of 97.8%. This technology is estimated to prevent approximately 2.2 billion won in raw material and production losses annually.
Professor Jung stated, “Unlike small-scale laboratory experiments, large-scale manufacturing involves significant costs to control quality and yield. Our AI-driven approach can be directly applied on-site to ensure stable, high-quality production.” He further added, “This methodology holds promise not only for battery materials but also for large-scale manufacturing sectors such as chemicals, machinery, and semiconductors.”
The findings were published in the prestigious international journal InfoMat (Impact Factor: 22.7, Top 3% in JCR) on May 8, 2025. This research was supported by the National Research Foundation of Korea (NRF), the Institute for Information and Communications Technology Planning and Evaluation (IITP), and the Ministry of SMEs and Startups (MSS) through various technology development programs.
Journal Reference
Junyoung Seo, Taekyeong Kim, Kisung You, et al., “High quality large-scale nickel-rich layered oxides precursor co-precipitation via domain adaptation-based machine learning,” InfoMat, (2025).